Should I use rubber, springs or wire ropes for anti vibration mounts?
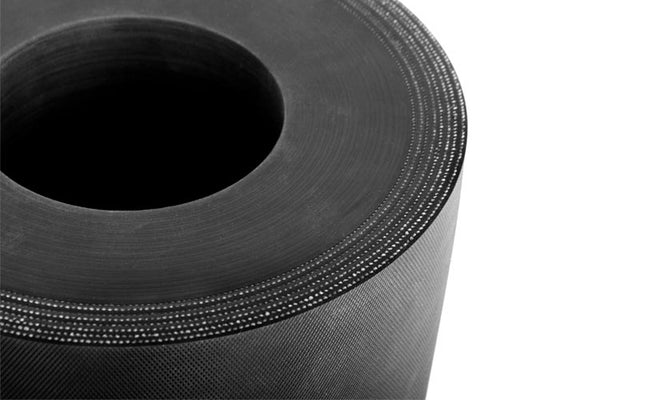
This is a common question, there are a wide variety of vibration absorbing mounts out there based on different materials – rubber/elastomers, metal (e.g. springs), foam, wire ropes.
If, like me, you grew up wondering what the answer to this question was, relax. Here is my view after many years in the industry. This article aims to tackle some basic differences and similarities between mounts based on these materials (there are other materials, but these are the main ones).
Summary of Vibration Absorption Media Strengths and Weaknesses:
*Whilst rubber can do a good job at both vibration and shock isolation, one product in is unlikely to be able to achieve both for the same application.
**Referring to solid, spongy foam. I am not an industry expert in foams, our key industry is in Rubber, wire rope and springs.
Rubber AV Mounts (often called Silentblocs):
Rubber is a generic category title, there are lots of different rubber types, some of which lend themselves to vibration absorption, some not so much. We will publish another article on rubber compounds in case you want to know more about this, but for now, we will refer to generic rubber based mounts.
Advantages:
- Cost: Rubber is probably the most common material that we see and use for AV mounts, for good reason. Once the product has been designed and mould tools manufactured, rubber offers great value for money.
- Built in damping: Rubber is essentially your spring and damper in one convenient package. Due to something called ‘hysteresis’, internal friction in the rubber absorbs energy and therefore brings oscillations to rest faster than would otherwise be the case. This also reduces resonance risks.
- Rubber works well in compression and shear (if Engineered properly).
Disadvantages:
- Needs more space: For a given space, metal springs will generally offer improved vibration absorption when compared to a rubber solution. Rubber tends to go stiff after 10-20% compression, whereas springs can compress much further before ‘bottoming out’.
The ‘operating window’ for rubber is a lot larger if it is worked in shear, either by rotating a standard mount or designing a more sophisticated mount. The disadvantage with this is that it needs more space. - Environment: It is important that potential exposure to solvents and fuels or oils is understood before picking a mount. The same can be said for high levels of ozone or sunlight. These are not a challenge, but the right rubber should be selected.
- Wide tolerances: Rubber can have fairly broad tolerances – the dimensional tolerances are generally less important, but the spring rate tolerances can be up to +/-20%. Tighter rubber and process controls can, in our experience, bring this down to +/-10%, but that is challenging. If spring rate requirements have to be tight tolerance, it is worth testing the products before using them.
- Temperature range: This is lower than for metallic media
Bracket examples for changing pure compression into pure shear, or mixing the two.
See our article on ‘what can go wrong with rubber’, to know more (this will be released in January 2023).
Wire Rope:
Advantages:
- Space required: The range of movement versus the space occupied is broadly in line with metal springs.
- Built in damping: One major advantage of wire rope mounts is the built-in damping.
- Flexibility: Wire rope mounts can be loaded in any axis, although for long term use one axis is not recommended.
- Environmental conditions: More stable than rubbers and foams, and able to handle a broader temperature range.
Disadvantages:
- Cost: Due to the considerable advantages of a wire rope mount, they are generally a little more expensive than other options
- Tolerances: A +/-20% spring rate is normal for wire rope mounts.
Metal Springs
Advantages:
- Wide operating bands: This has to be one of the biggest reasons to use springs. They typically compress 50 – 80% of their height, and compression matters when it comes to vibration and shock absorption.
- Relatively tight spring rate tolerances (typically +/- 5%)
- Can be used in compression and tension
- Environmental conditions: More stable than rubbers and foams, and able to handle a broader temperature range.
Disadvantages:
- No damping: For most industrial applications we consider this a disadvantage, although it could be argued that the lack of built-in damping allows more precise damping to be selected and implemented with a specialist product. That is certainly true for vehicle suspension, but rare in industrial applications.
- Shear loading: Springs are generally not loaded close to pure shear, their fixtures are also rarely designed to handle this loading either.
- Cost: Whilst springs are less expensive than wire rope mounts, they are typically more expensive than rubber options.
PLEASE NOTE: This article has been produced quickly, which the intent of helping the reader. Apologies for any spelling errors, if you have any questions, drop us a line.