Rubber Product Tolerances
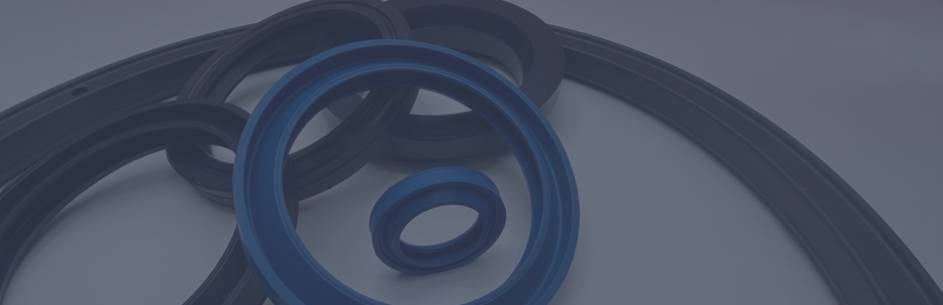
What tolerances should I use for Rubber Moulded products?
Rubber Moulding Tolerances:
If you are developing a custom or bespoke rubber moulded product, it is useful to understand what typical tolerances are in the industry. This is a common question.
It is worth stating that
- AVMR are comfortable to work to tighter tolerances, but this is rarely required.
- We are just talking about dimensions of rubber elements here, not the parts that they might be bonded to. This might seem obvious, but it is worth being clear.
Tolerances are generally defined as M1 to M4 (M1 being the tightest), as in the table below. We do see tighter tolerances than M1, but they are either used by accident, or for less cost sensitive applications, where precision really matters.
For Rubber Moulding, the relevant standard for linear dimensions is BS ISO 3302-1:
Tolerances are separated into fixed and closing dimensions, with the latter being a little ‘looser’. See the bullet points, below, for more information.
To reliably be tighter than M1 requires controls beyond those found in typical moulding processes and materials used. Tighter tolerances are absolutely possible, but rarely required or justified.
We (AVMR.com) typically mould to M2 as our tooling is precise and well planned, but we quote M3 unless tighter tolerances are required.
What impacts Rubber tolerances?
A very good question. This generally comes down to managing volume change, the curing process, and controlling process inputs:
- Thermosetting elastomers (e.g. rubber, silicone and polyurethane) generally grow in volume during curing before shrinking once vulcanised and cooled. The final volume is typically around 2% lower than the initial volume.
- Substrates: If there are metals or other substrates in the product, they might prevent contraction from happening in some areas and encourage it is others.
- If moulding a cube of rubber, it should shrink fairly uniformly, but if one side is bonded to a plate, that plate will probably restrict shrinkage of the rubber immediately bonded to it. The result being that:
- shrinkage might be exaggerated in other places
- a level of tension or stress is likely to remain in the product along the bonded interface.
- In a double or triple bonded bush, there will be no measurable radial shrinkage but exaggerated axial shrinkage. We consider it important to stress relieve rubber in bushes, where possible, as without it the rubber is in tension in all 3 axes. This leads to
- micro-fractures on the surfaces which have a significantly higher surface area open to attack from ozone, sunlight etc.
- a bond interface with greater forces on it that necessary
- Bumping: as rubber vulcanises it produces small volumes of gas which are generally allowed to escape from the mould tool. This escape is facilitated by ‘bumping’ the mould tool during the early stages of the curing process. Bumping is the full or partial removal of pressure holding the mould tool closed for a short period of time (fraction of a second) before reapplying the pressure. This allows the mould tool to open up just enough for gas to escape. This is not always necessary.
- This process drives the different tolerances for dimensions which are impacted by the tool being opened and closed (closing) versus those dimensions which are fixed.
- Shape factor: Working out which dimensions are likely to shrink can be challenging. In a simple O-ring, or a donut shaped item, the centreline circumference of the ring may will shrink by circa 2%, as will the cross-section. This means that while the inner diameter of the O-ring may well remain fairly constant the outer diameter is likely to shrink by over 2%.
- Material properties: Different rubbers will have different shrinkage rates – 2% is just a typical value.
- Different batches of the same rubber will have a variation in acceptable material properties. For example, typical British and European Standards quote a +/-5° on hardness for ShA or IRHD when the nominal value could be 35°. That is a significant range for the given nominal value. The knock on impact of these material tolerances, is a range in factors such as shrinkage.
- Moulding parameters: The approach taken to moulding, the mould tool design and the process parameters can also have an impact.
For more information, please drop us a line, or fill out the contact form on our website.
Kind Regards,
Daniel & the team at AVMR.