06/26/2023
Heat Generation in Rubber and Elastomers
Introduction
A customer recently asked us to help them understand why a competitor rubber product was failing prematurely. The rubber within the product was cracking and almost turning to dust well before it should have done. The answer came down to product design and material selection. It was heating up a lot in its application, and the result was that it was ageing prematurely.
Heat within rubber products can be a challenge. Understand if it is going to be an issue, and design around it. We are here to help.
Why does rubber generate heat when it is deformed?
As rubber is deformed, it generates heat. This is a side effect of rubber’s popular visco-elastic properties. As in a rubber car tyre, after 10 minutes of driving the tyre will be warmer, it will continue to heat up until it is losing heat at the same rate that it is being created.
Why does this happen? Rubber has elastic properties which allow the material to stretch or squash before returning to its original shape (normally). However, it also has viscous properties which act as a damper and dissipate some of the energy generated by the stretch, or squash, in the process. That dissipated energy is primarily turned into heat.
Why does heat generation in elastomers matter?
For certain applications, heat generation is negligible and does not matter, but for other applications it really does matter. In something like a static seal, there is negligible generation due to negligible rubber motion, while in a car tyre or shaker table connector there can be lots of heat generated due to lots of motion. This heat generation needs to be managed.
As rubber heats up, it becomes softer. This can change the frequency of a shaker table, or make a tyre have more grip on the road. If a rubber compound operates in an environment that is towards its maximum continuous temperature, once heat generation is added to the mix the temperature within the product can breach the maximum continuous temperature for the material. If this high temperature is sustained in part of the material, breakdown of the rubber can be initiated.
Rubber products which generate heat can also experience accelerated aging. Rubber ages with time, and the amount of time is shortened by increased temperatures. Rubber is an insulator, so the middle of the product can be much warmer than the surface if the wall thickness is large.
What impacts the amount of heat generated in rubber?
There are two key application related factors which impact heat generation, they are the amplitude of the deflection and the frequency.
Deflection
If you imagine a car tyre, it will not deform much when driving if the tyre is fully inflated however, it still generates heat. When it is only partially inflated it will deform a lot more and generate a lot more heat. The amount of heat generated from the rubber is therefore related to the amount of deformation, or deflection.
In a rubber anti-vibration mount, the same can be said regarding the amplitude that the vibration mount. The greater the amplitude that the mount experiences, the greater the amount of heat generation. Again, the amount of heat generated from the rubber is related to the deformation, or deflection experienced.
Frequency
If a car drives faster, more heat is generated by the tyres. Each turn of the tyre deforms the rubber, and the rubber absorbs a certain amount of energy. If the tyres turn faster there is more energy to be absorbed as more deformation happens.
In Formula 1 racing, a car tyre is under maximum load when the car is travelling fastest, the tyre is therefore deforming more at high speeds (ignoring technologies like DRS). The tyre is also being deformed at its highest rate, or frequency. Therefore, most heat is generated in a tyre at high speeds.
Thermal conductivity
All elastomers are poor conductors of heat with K (thermal conductivity) being low at 0.2 – 0.3 W/m°C. Therefore, heat generated far from a heat “sink” can become locked in and take a significant amount of time to dissipate.
Adding a good conductor to the polymer compound will help with thermal conductivity, but they do not give a significant improvement. The additive becomes encompassed in the polymer and therefore prevent good conductive paths from being built.
Equations for heat generation
There are equations which can be used to estimate heat generation, these will be discussed in a further article.
In the meantime, the key variables on heat generation are:
- Rubber wall thickness
- Ambient temperature
- Thermal conductivity of the material
- Energy absorption of the material (a viscous property)
- Frequency of oscillation
- Amplitude of oscillation
How should Heat Generation be measured?
The best way to measure heat generation is by using the simplest approach; in an actual product in the actual application. By taking temperature readings from the surface of the product before the test starts and during the test, the level of surface temperature increase can be measured.
By creating a small hole to the thickest part of the rubber body in the product before the test, a probe can also be regularly inserted into the centre of the product to take further readings. Although these will only be indicative, they the indication will be important. It is worth being able to close this hole (e.g. with flexible tape, or a rubber ‘stopper’ to improve this reading. It is worth nothing that the small hole should be carefully positioned so as to give the smallest impact on performance.
More sophisticated measurement approaches are available, but the above approach works sufficiently well for most applications.
Managing Heat Generation
Shaker tables, or shaker machines, need careful consideration of heat production when selecting or designing mounts.
Options to reduce this heat relate to the key variables given above, and include:
- Designing the product to have a thinner wall.
- Adding holes to the product to enable heat to escape.
- Adding a metal substrate, or matrix to conduct the heat away.
- Metal or graphite additives can be added to the rubber.
- Use a stiffer rubber (assuming that this is in an application which will allow it to reduce the amplitude of the oscillation).
- Use a softer rubber (assuming that the amplitude is fixed).
- Use a material with a lower loss modulus (assuming that the amplitude is fixed).
If you have questions about an application where heat generation could be an issue, drop us a line, I am sure we will be able to help you.
Related Posts
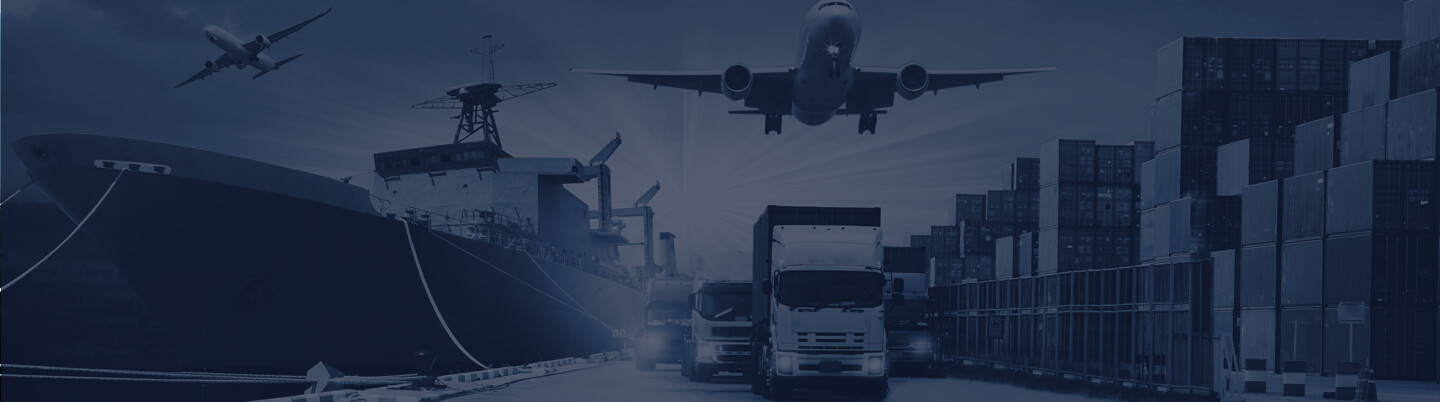
07/03/2023
Challenges in specifying Rubber and Elastomeric Materials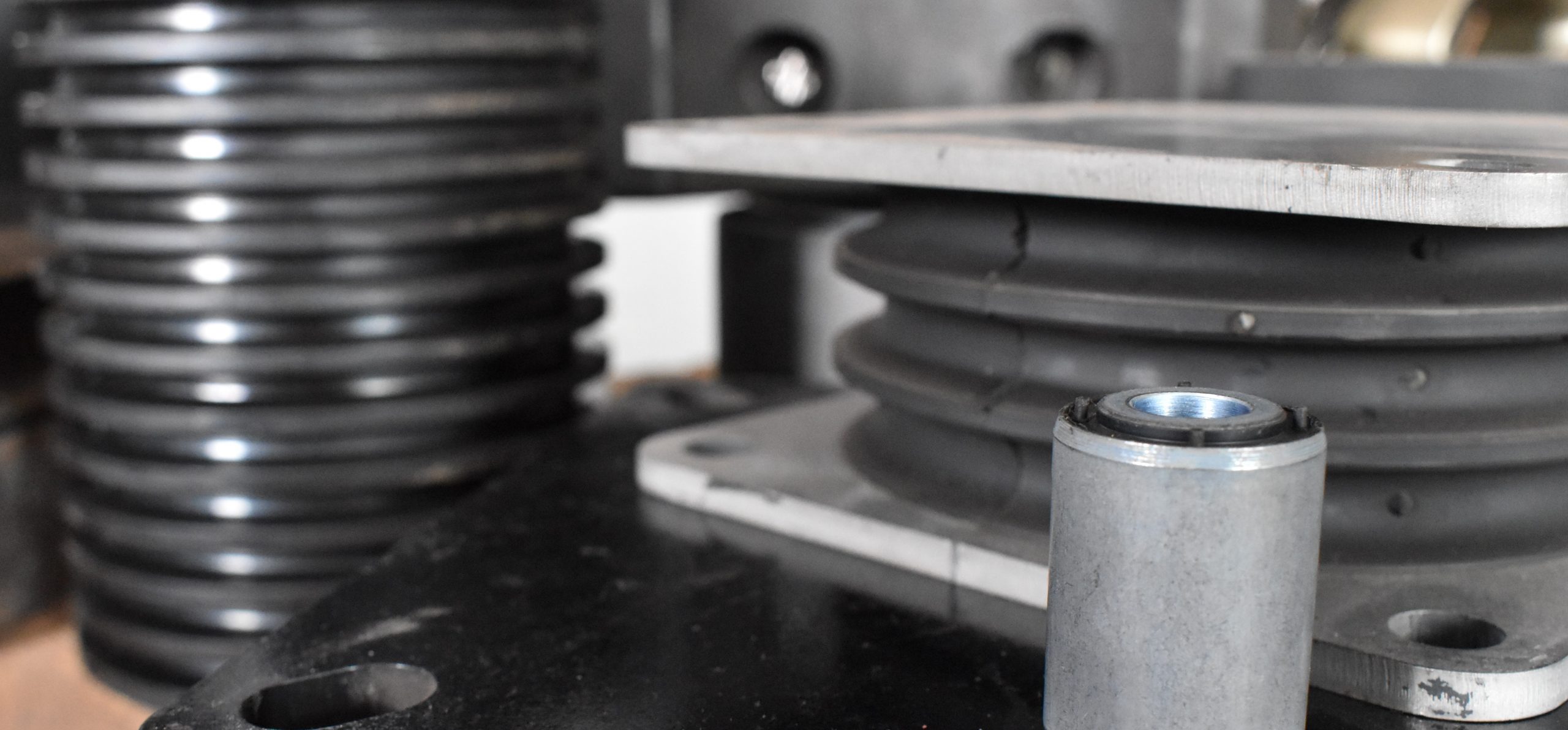
07/03/2023
Natural Rubber Engineering Compounds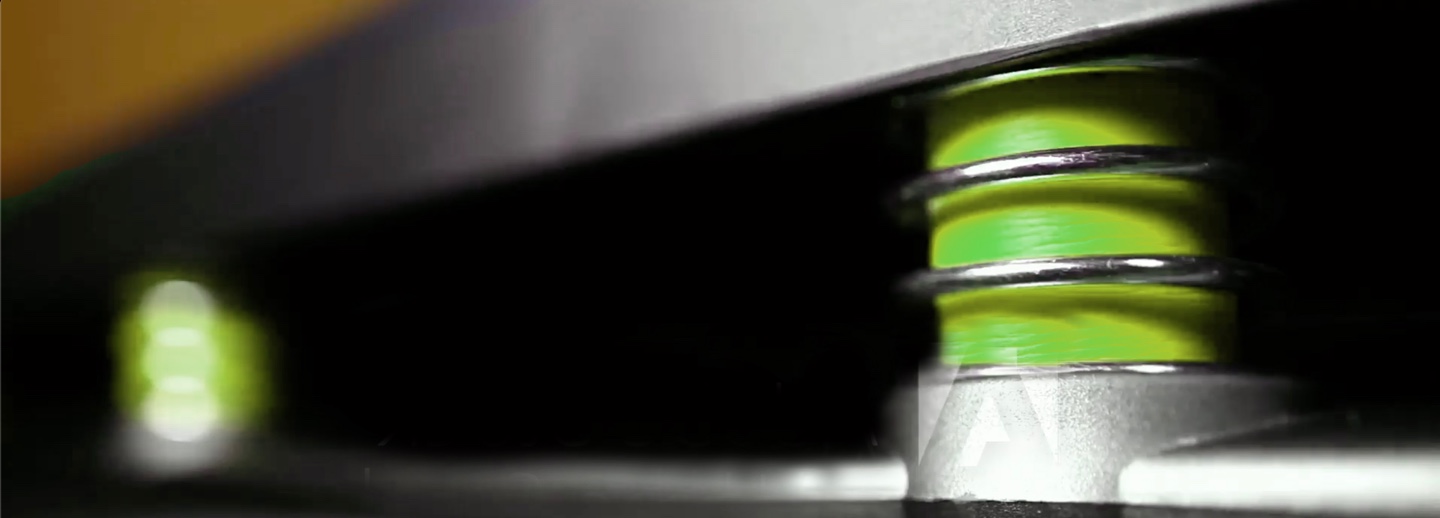
06/26/2023
Heat Generation in Rubber and Elastomers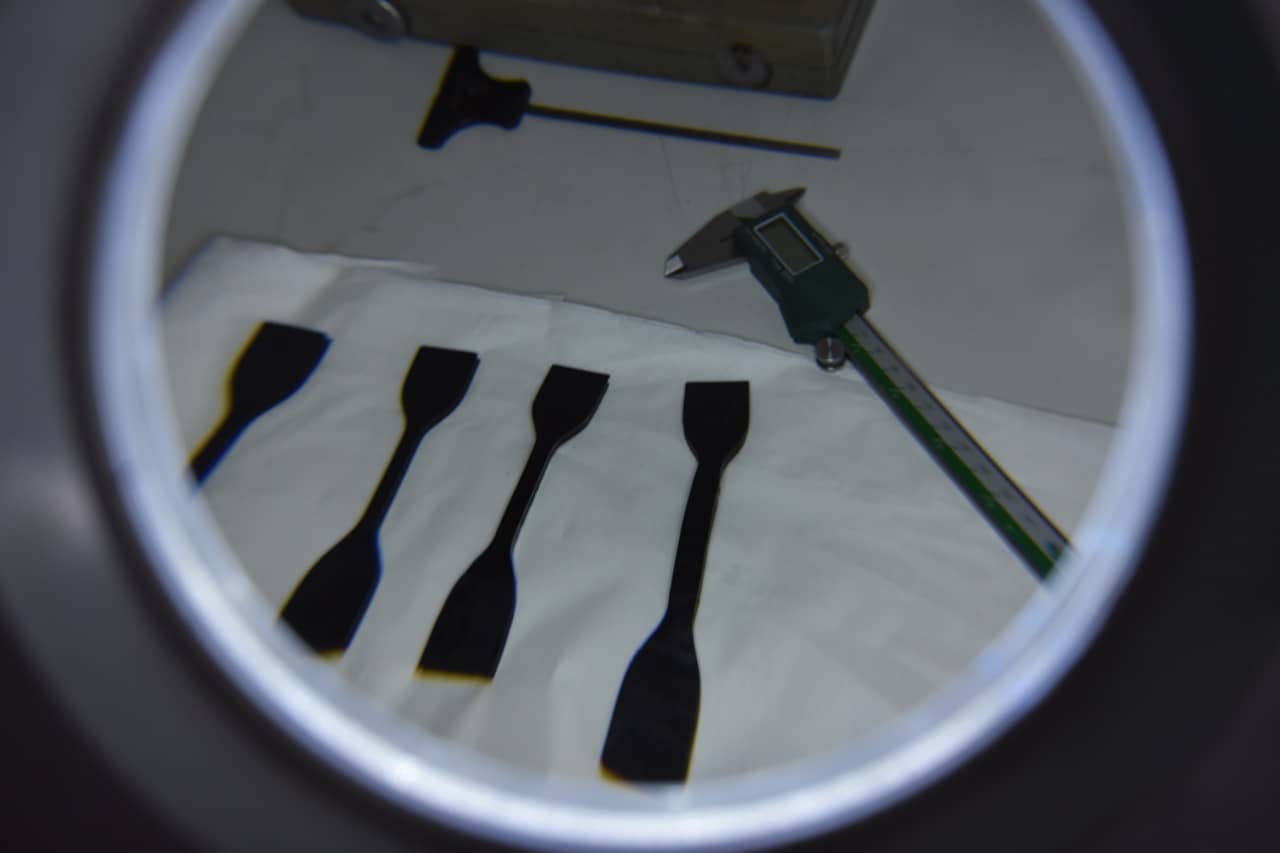
06/12/2023
Stress-Strain Characteristics of Rubber & Elastomers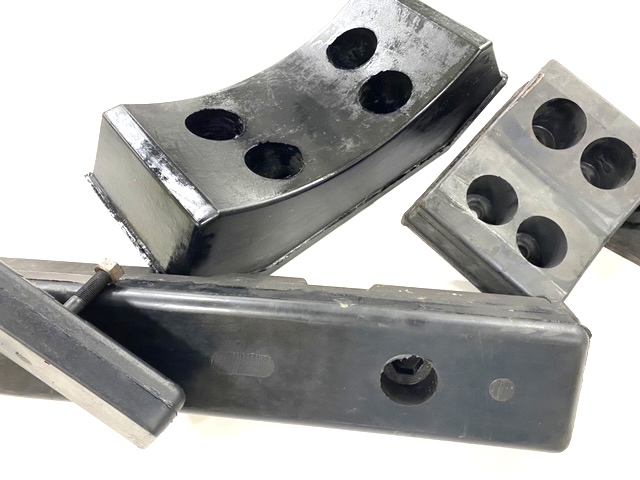
05/22/2023
How to create a strong rubber bond in my product?