07/03/2023
Natural Rubber Engineering Compounds
This article is brought to you by AVMR.com, specialists in rubber moulded Engineering products and vibration control.
If you are designing a rubber Engineering product, contact us by clicking here, we like solving interesting challenges and will be happy to help, or point you in another direction.
Introduction
The technical name for Natural rubber (NR) is Polyisoprene, it is made from a series of isoprene blocks joined up into a chain.
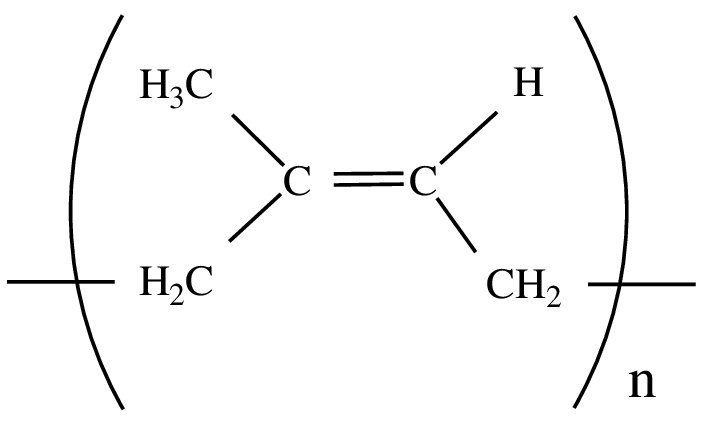
Hello, I am isoprene (C5H8)n, the basic building block for Natural Rubber
Natural rubber is one of the most widely used compounds in Industry due to its high performance in certain areas. However, it also has notable weaknesses; use it in the wrong place and there will be trouble.
Selecting the right polymer for an Engineering product is the first 20% of the material design challenge, managing its weaknesses and ensuring consistent performance is the remaining 80%.
You can find a table comparing the high-level properties of different rubber polymers here. The aim of this article is to offer a little more detail on considerations AVMR make when selecting and designing a Natural Rubber compound for Engineering products.
Key benefits of natural rubber in Engineering
Key benefits of natural rubber compared to other rubber/elastomer polymers include
- High strength – high abrasion and tear resistance
- Outstanding fatigue resistance
- High resilience (ratio of energy returned upon recovery from deformation to the energy required to produce the deformation)
- High range of hardnesses
- Low sensitivity to strain effects when in dynamic applications
- Good compression set
- Good creep resistance
Therefore, NR compounds can, by design, have a combination of a low modulus, high strength, low damping and fatigue resistance. If you are into rubber engineering, it is pretty cool, and why NR is so popular for vibration absorption (attenuation) products like mounts, bearings and bushings (bushes, silentblocs, spherical bearings).
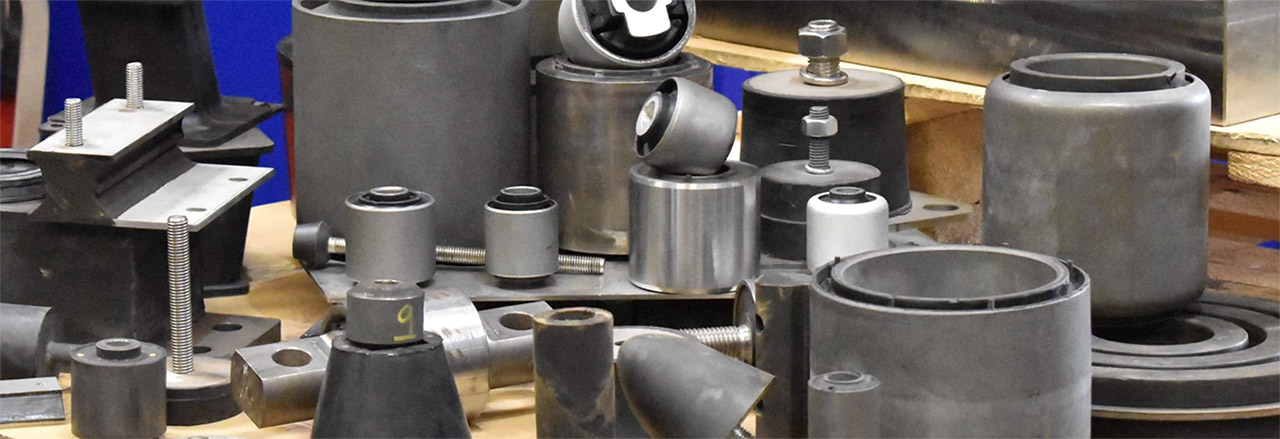
AVMR.com: AVMR understands Rubber material selection & detailed design challenges
Weaknesses of natural rubber in Engineering
There are weaknesses, or limitations to Natural rubber when compared to other elastomer compounds. AVMR designs and manufactures particularly precise and tight tolerance products and, from our Engineering perspective, one of the key challenges relates to it being a natural product.
Natural rubber is produced from latex, which comes from trees (the Hevea Brasiliensis tree). As it is a natural product, there is variation in its properties from batch to batch. In soft rubber products this latex can make up to 80% of the compound (the material we make products from), therefore the compound is sensitive to the properties of the latex. As a result, tolerances for certain characteristics in soft compounds are broad and can only be refined by an iterative material production (compounding) process, which can be challenging and therefore expensive.
The key to material control for NR is dilution – not enough to lose its key properties, but enough to introduce more controllable diluents.
In higher hardness compounds, the latex is essentially diluted with other materials to generate the required properties. As the latex is diluted the variation its properties become more diluted therefore making it easier to create a more tightly controlled product.
Through blending the NR with other rubber polymers, we can also increase control. Car tyres use NR with highly repeatable results, they do this through blending the NR with synthetic rubber polymers, and we do the same.
Other typical weaknesses or limitations of Natural Rubber include:
- Low resistance to organic fluids and oils
- Low maximum working temperatures
- Low resistance to ozone, oxidation and weather, although additives and certain production techniques can be used to significantly improve performance.
You can find a table comparing the high-level properties of different rubber polymers here.
Next Steps
If you are designing a rubber Engineering product, contact us by clicking here, we like solving interesting challenges and will be happy to help, or point you in another direction. We are rubber design and moulding specialists.
Related Posts
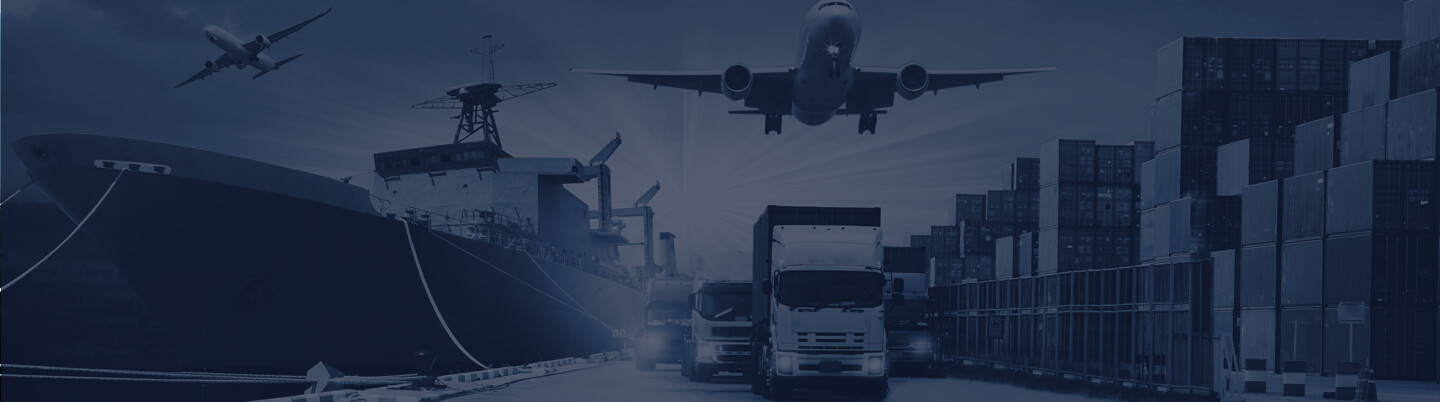
07/03/2023
Challenges in specifying Rubber and Elastomeric Materials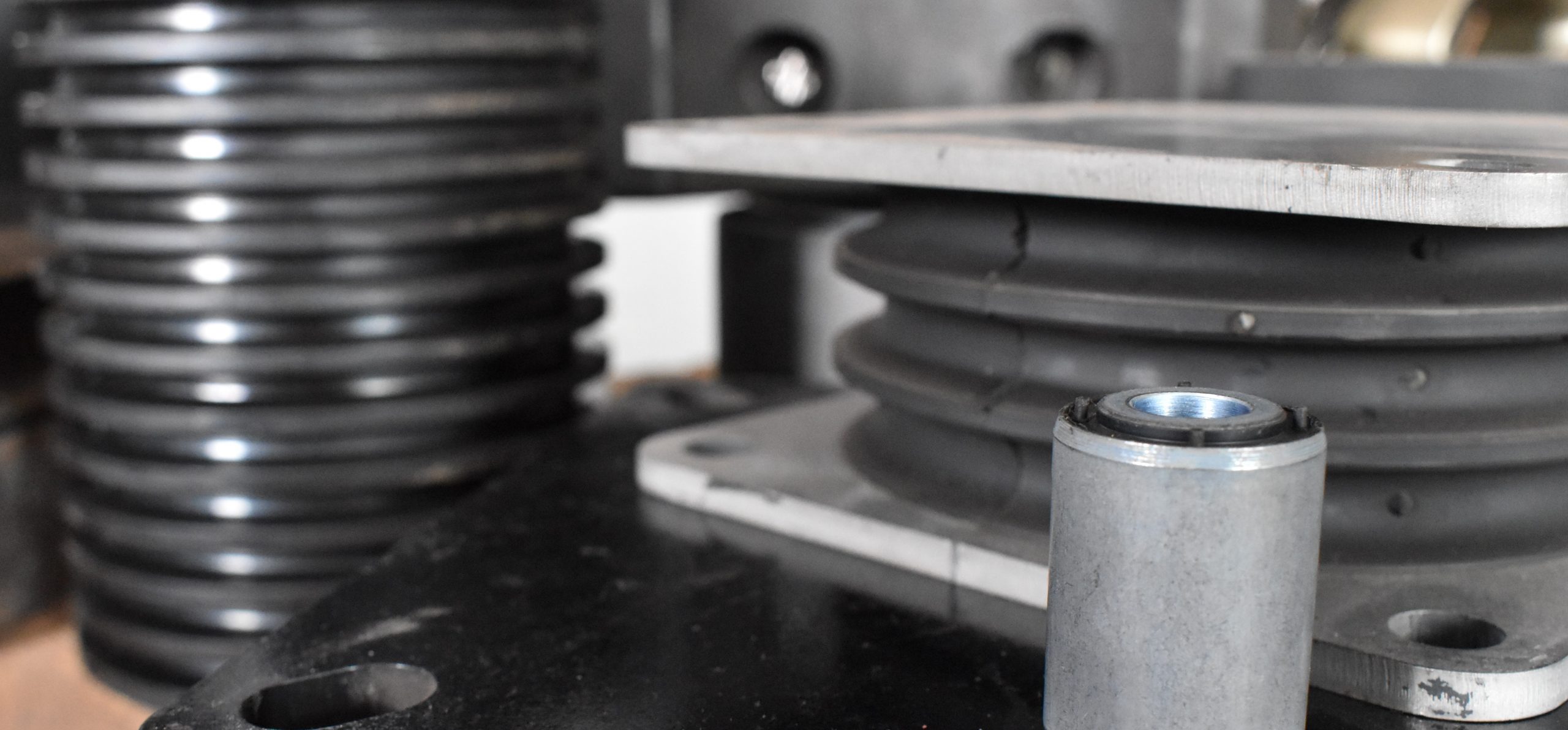
07/03/2023
Natural Rubber Engineering Compounds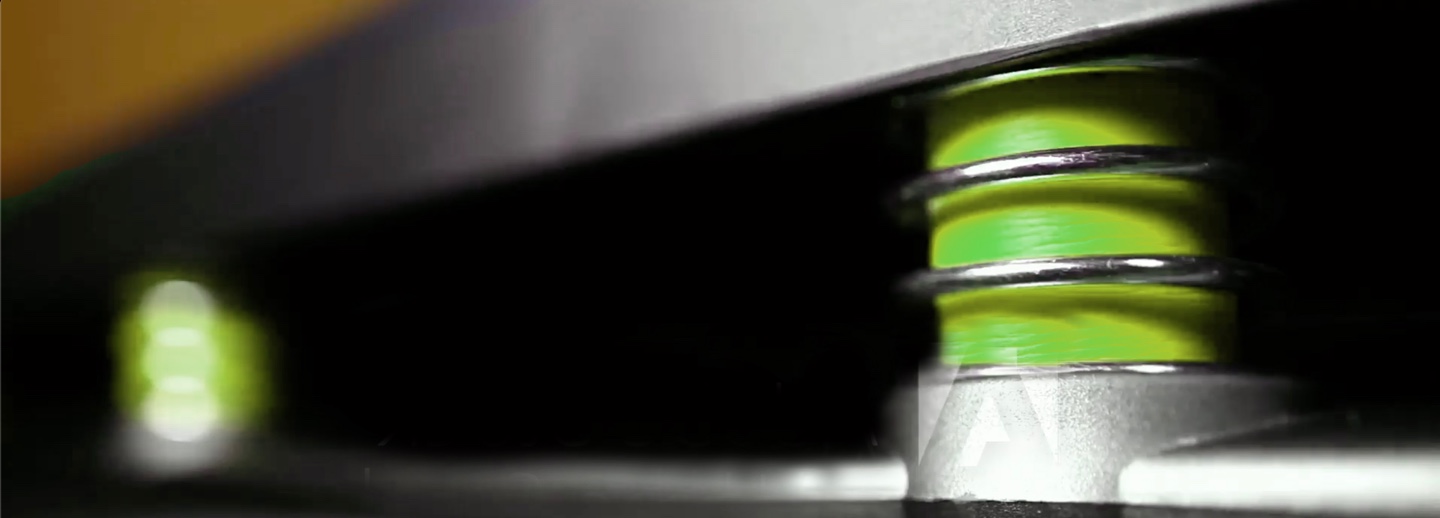
06/26/2023
Heat Generation in Rubber and Elastomers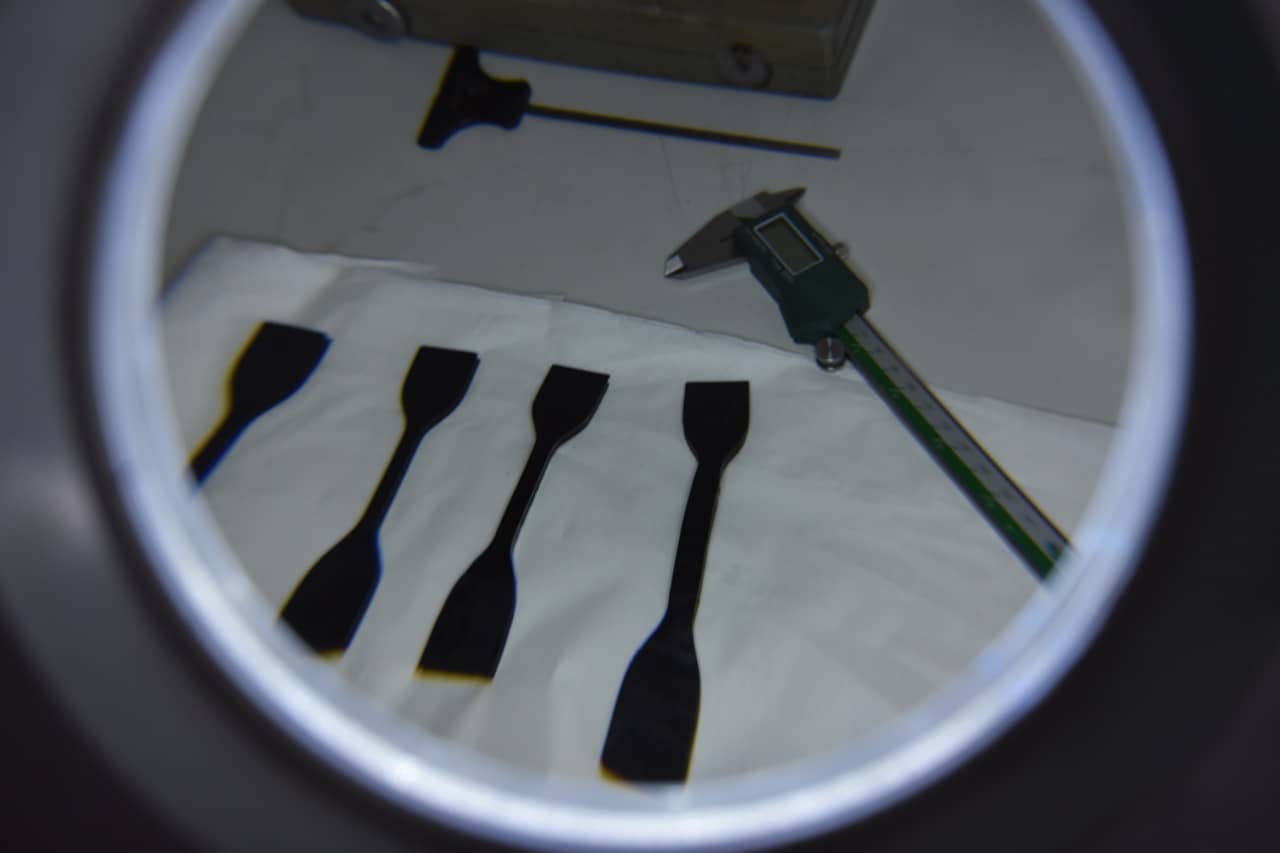
06/12/2023
Stress-Strain Characteristics of Rubber & Elastomers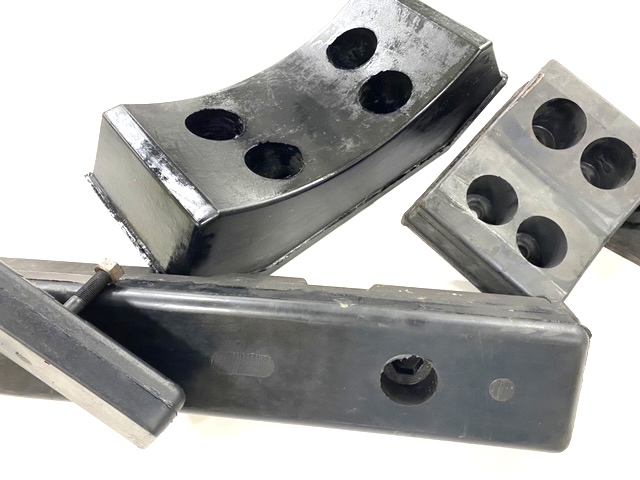
05/22/2023
How to create a strong rubber bond in my product?