05/22/2019
A Guide on Bushing Designs
At AVMR we have spoken to experienced suspension designers who have shown frustration at the design compromises they have had to make when using bushings. However, it’s apparent there is often a lack of awareness regarding the readily available design options there are to overcome common challenges. Here’s some advice when considering differences in bushing design.
At the simple and low-cost end of the spectrum there are basic rubber-only bushings. These are normally used only in very light applications which involve little or no torque.
Photo 1: a simple rubber bushing.
When bushing interfaces slide, we would start adding tubes, or substrates to the design – initially to the inside face, then also to the outside face. These tubes are normally either bonded to the rubber, or an interference fit. The tubes do four things:
- Encourage uniform deformation of the rubber element to the bushing.
- Protect the rubber against wear from sliding interfaces. The insertion process can be one of the most damaging events in a bushing’s life.
- Provide an anchor point.
- Provide a bridge. For example, from a very narrow outer clamp to a wider rubber element.
Tubes can also be a sliding fit, which provides some of the above benefits, however that is not normally the case.
In order to help with insertion, outer tubes can be chamfered or peened. Peening also restricts axial deflection which might be attractive, especially if the outer tube is just an interference fit to the rubber element rather than bonded.
The Fixtures
The simplest way of fixing a basic bushing in place is through friction; by clamping it, or by using an interference fit.
For the outer tube, an interference fit into an outer casing on a chassis or suspension arm is by far and away the most common option. For higher rotational loads friction can be increased by:
- Increasing the level interference in the fit.
- Increasing the wall thickness of the outer tube which increases the resistance to compression in the interference fit.
- Increasing the outer diameter of the bushing.
- Using a higher friction surface finish.
- Bonding the bushing into place. Less common now than it used to be.
If the above options fail, then mechanical locks will be used, but this is rare in vehicles – even in trains and heavy goods vehicles, friction is normally sufficient to hold the bushing in place.
In our experience, mechanical locks will be introduced in either some industrial applications, or in smaller applications where the outer tube provides additional functionality, such as a mounting point.
Photo 3: A flanged bushing with mounting bolts included.
The inner tube is normally clamped to an outer bracket, or suspension arm, using a simple nut and bolt down the middle of the tube.
Friction might not work for higher load applications which cannot tolerate slippage. If one interface is likely to slip, it is normally the inner tube. So, mechanical locks are commonly employed here.
Typically, the following methods are used to fix the inner tube in place:
- Friction.
- Higher friction finishes to the tube.
- Knurled ends to the inner tube. This should be done in combination with a mirrored interface for the knurls to lock into, without this mirror we find that the knurled finish adds little value. Knurls range from being shallow to heavy castellations.
- A Keyway. This enables tight positioning and a robust rotational lock in a fairly compact product. As in this example, the shape of the inner tube provides some of the properties of a ‘bellied’ inner tube (see section on spring rates), if required.
- Bolted to prevent any rotational or axial movement. This is commonly used in heavy goods vehicles, buses, and industrial applications, but can also be found on high-end lightweight applications. One advantage of this fixture methods is that it can be loosely aligned, and then tightened into place.
Photo 6: A typical HGV bushing with bolt points.
Taper locks can be used for both inner and outer tubes, and they provide two really useful features:
- They enable easier insertion and removal than constant diameter tubes when using an interference fit. This is particularly useful on the production line or when bushings are being replaced.
- If bushings are orientated vertically, taper locks prevent axial slippage.
Spring Rates
The whole purpose of the bushing is to attenuate vibration and to absorb shock, and that is done using the rubber element of the product. However, common approaches to improve performance in one degree of freedom will negatively impact performance in other degrees of freedom.
Therefore, it can be important to use a range of methods to gain the required result:
- Dimensions
Varying the internal and external diameters, and therefore the rubber wall thickness, and the length of the rubber element have the greatest impact on the final product.
- Rubber Hardness & Modulus
Material spring rates can be adjusted by adjusting the rubber used. It is also possible to have different rubber compounds in different areas of the bushing, but that can become expensive quickly.
- Cavities
These are important and commonly used, as there is little impact on ongoing cost and it reduces weight of the end-product, so this is often seen as a sensible investment to make.
Cavities within the rubber bushing can be positioned to impact spring rates in some directions whilst having little impact in others.
It is worth noting that cavities can become complicated quickly. They can be incredibly effective and are much more than just simple gaps in the rubber.
Photo 7: A Meyle rubber bushing with a complex cavity design.
- Inserts
Inserts can be used to restrict movement in some directions. For example, a third tube in the bushing has little impact to rotational stiffness but doubles radial stiffness.
Photo 8: Triple bonded rubber bushings. The third tube is a simple insert.
- Irregular tube shape
‘Bellied tubes’ or ‘flared tubes’ are a lower cost way of using certain types of insert. However, they come with a potential cost of reduced strength to resist high axial clamping forces.
Photo 9: Bellied inner tubes.
An example of a common issue:
A common problem in suspension design is how to design a bushing which will allow large amounts of rotation without allowing too much movement radially, which is important for alignment in road cars.
Note: In off-road cars radial compliance is potentially the more important requirement.
In wishbone suspension this would translate to the suspension designer wanting to have free wheel movement vertically (rotation of the bushing) without having potential wheel alignment issues (radial movement of the bushing).
A common decision is to compromise the vertical movement by using a stiffer, smaller diameter bushing, but there might be a better solution which could include:
- Increasing the rubber wall thickness of the bushing, which will allow more movement.
- Using inserts or an intermediate tube can double the radial stiffness whilst having a minimal impact on rotational stiffness.
- As per the above point, a ‘bellied tube’ can reduce the soft radial spring rate which comes with increased rubber wall thickness.
- Using rubber cavities in non-critical areas of the bushing. This can greatly enable rotation whilst having a relatively small impact on radial movement.
- Using a softer or harder rubber compound with any of the above tools can further help refine the deflection properties of the end-product.
Managing Product Weight
Weight is becoming increasingly important due to its links to fuel consumption and handling. Naturally, the weight of the product is impacted by both the amount of material used, and material selected.
Weight can be reduced by:
- Using cavities in the rubber, in combination with a stiffer rubber rather using additional inserts.
- Using alternative substrate materials, e.g. aluminium or plastic as opposed to steel.
- Reducing the wall thickness of the substrate, potentially in combination with using a higher strength material. One challenge with thinner wall sections on metal substrates is corrosion resistance.
Corrosion Resistance
Corrosion resistance is, naturally, important. Commonly available options that we use for steel substrates offer up to 1,000 hours of salt spray corrosion resistance, which in our experience, is about as high as anyone will ever require.
Alternative substrates to steel are also worth considering, common options include plastics, aluminium and stainless steel.
When looking at various plating options it is important to consider:
- The required level of corrosion resistance.
- If the bushing is to be stress relieved (required for long-life bushings), the plating will have to be flexible. Many platings are compromised as they fracture during this process.
- Friction is an important factor, as discussed above. The wrong plating can effectively lubricate the interface.
- The plating must work with typical bonding agents. Not all plating options can be bonded to.
In summary, choose carefully!
If you need more advice on the bushings that are available or can be created for your needs, please drop us a line at sales@antivibrationmethods.co.uk or Tel: +44(0) 1985 219 032. We’re happy to help.
Related Posts
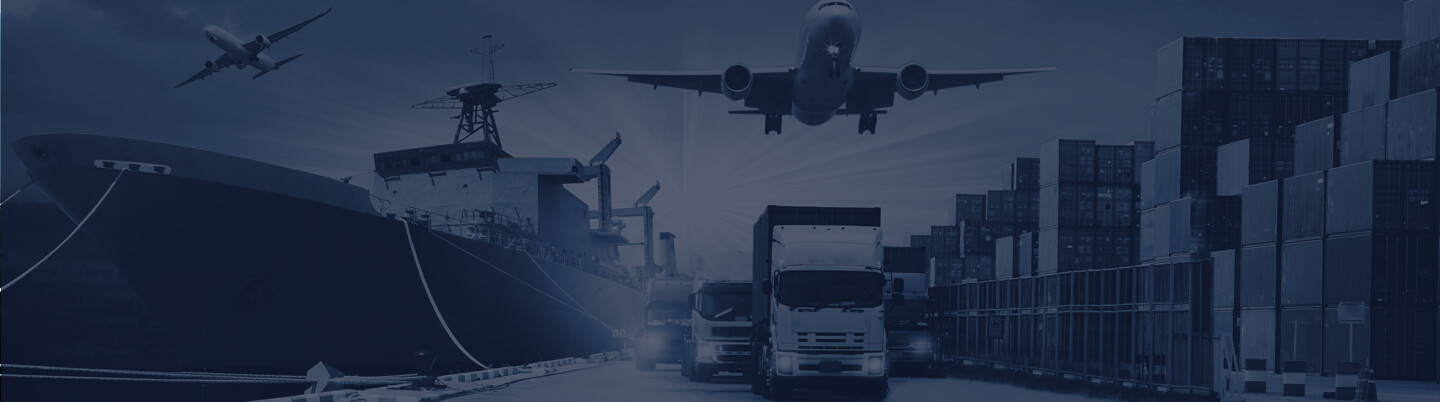
07/03/2023
Challenges in specifying Rubber and Elastomeric Materials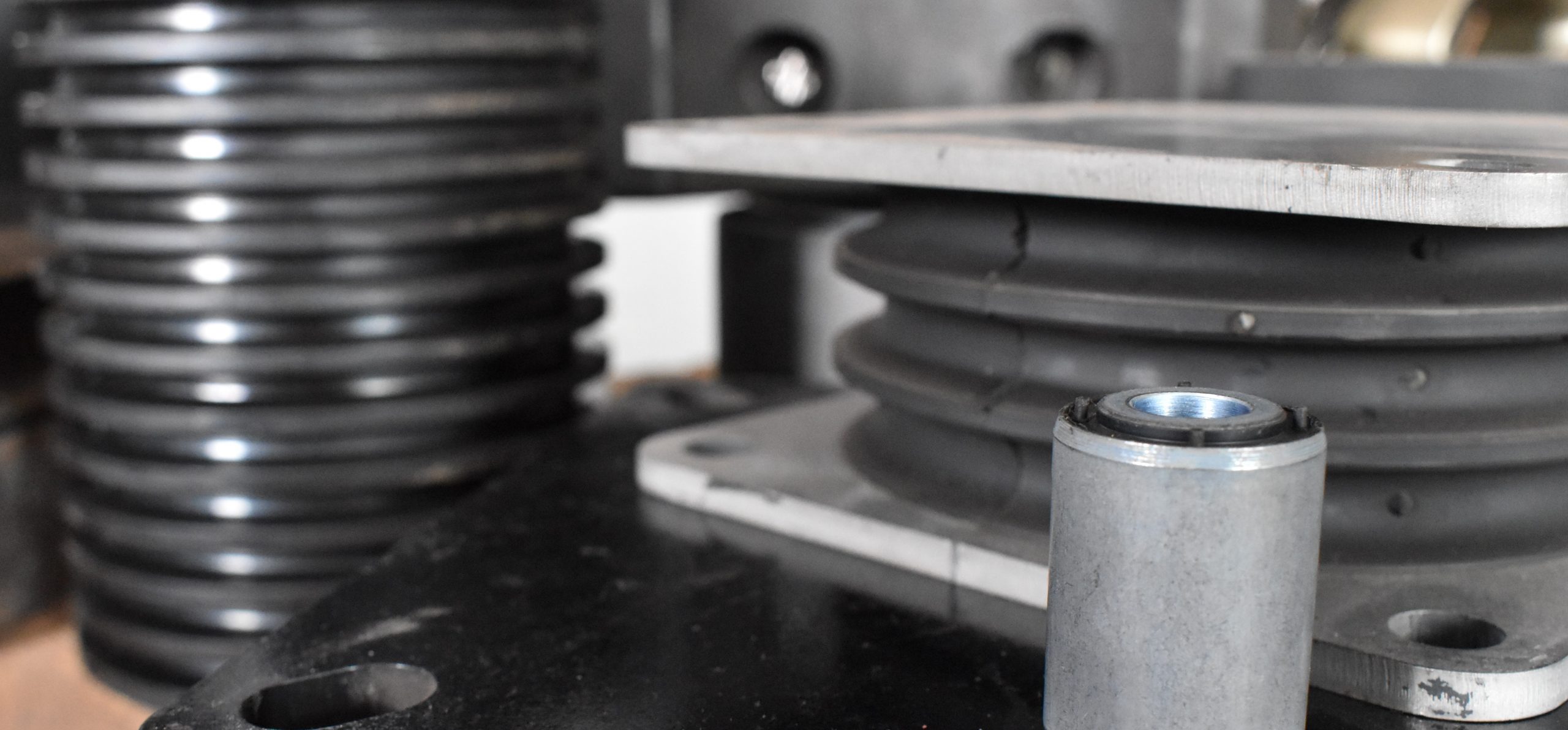
07/03/2023
Natural Rubber Engineering Compounds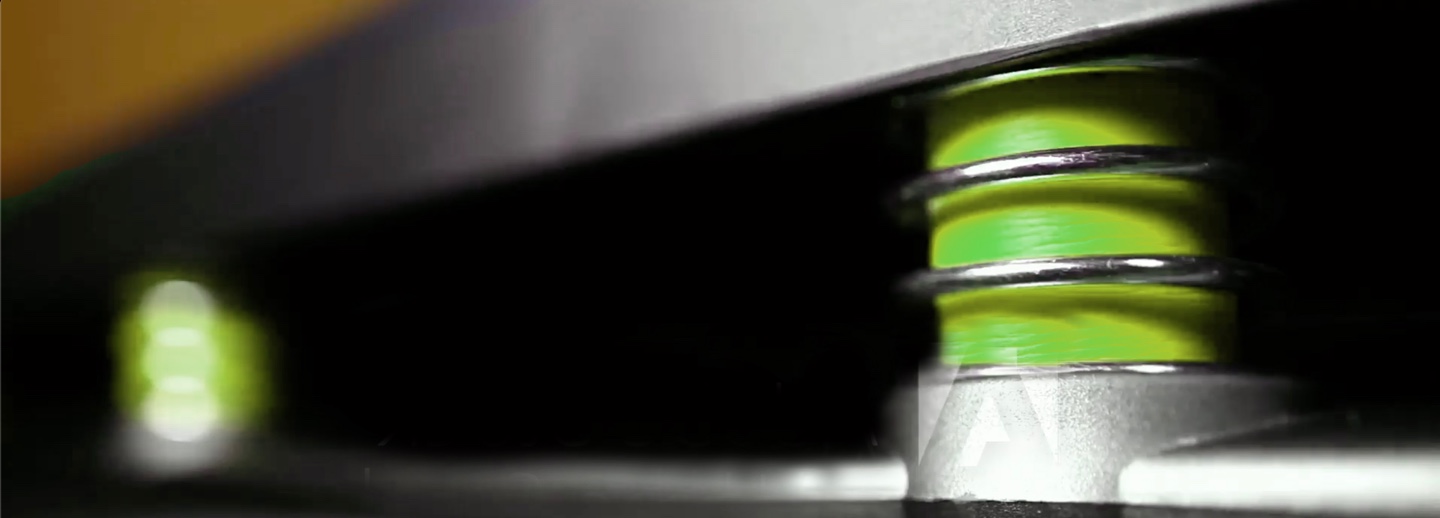
06/26/2023
Heat Generation in Rubber and Elastomers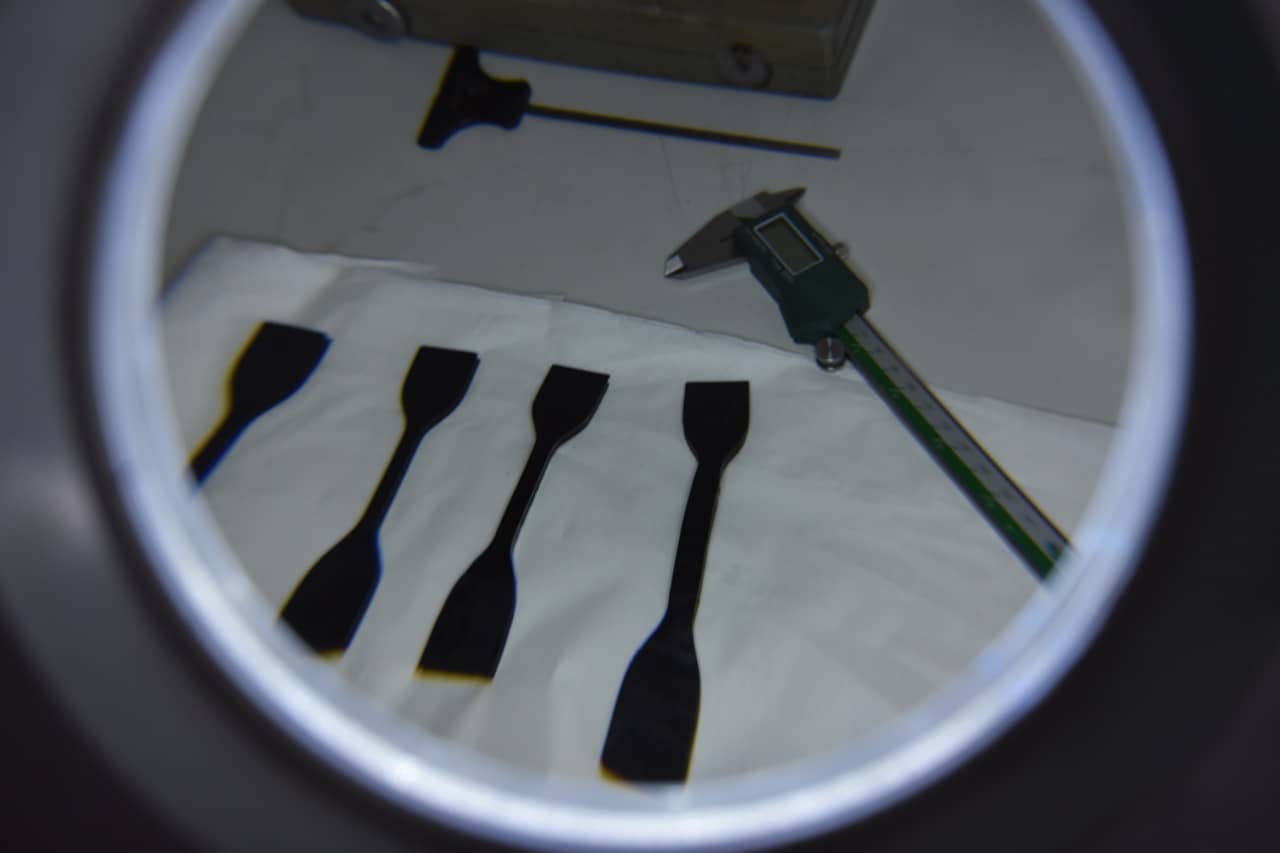
06/12/2023
Stress-Strain Characteristics of Rubber & Elastomers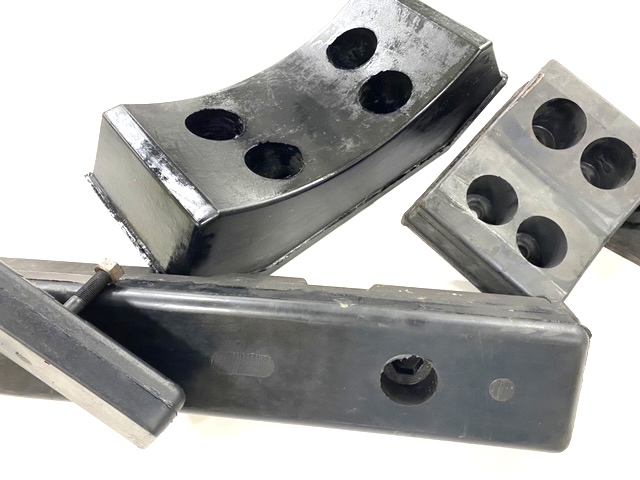
05/22/2023
How to create a strong rubber bond in my product?