06/12/2019
Getting Rubber Right
Rubber compounds vary, so do operating environments. Why hope that a conveniently available option will work, when you can be confident that a tailored option will?
It’s a fact that every creation is secretly only as good as the sum of its parts. We all know the notion of the weakest link. But all too often the most vital component of a suspension system is given the least amount of thought.
Detail is everything for rubber selection
Take that simple piece of rubber hidden deep within your industrial or automotive project. Pretty inconsequential in the scheme of things? Something that can be bought off the shelf, guaranteed to work and always be ‘right’? After all, rubber is rubber. Right?…
Not so. In our experience the primary cause of product failure can often be traced back to simple rubber selection.

Above: Daniel Lawes showing in a filmed experiment (coming soon) how conditions can impact on the wrong rubber choice.
Rubber is rubber? Well, the main component of any rubber is its base. There are five commonly used base rubbers, but specialists can offer up to 15. Then there are fillers that can strengthen. And fillers that can cheapen. Accelerators and retarders that change the rate of curing. Plasticisers to help materials flow and slide. Protection to shrug off extreme temperatures, ozone, UV light. And even colours and odorisers to make it look and smell good… These all combine to give each rubber a unique personality – one that’s truly tailor-made for just one job.
You may need a perfect seal – a rubber that can bounce back after years of compression. Or a rubber that’s tear and abrasion-proof for use in a traction pad or resilient AV mount.
Then there are the worries of location, extreme weather, exposure to chemicals, flames even…
Above: Adding extreme heat or solvents may make a typically robust rubber considerably weaker. It pays to select suitable properties for the rubber, early in the project.
Advanced rubber chemistry
For example, there’s the work we’ve done with well-known supercar designers. Working with our polymer scientists we devised an exhaust mount capable of withstanding some of the highest temperatures that rubber polymers have ever worked in. We accomplished this thanks to our understanding of advanced rubber chemistry, airflow and heat shields.
Similarly, we identified a no less extreme problem associated with the persistent failure of golf carts in Dubai. The original bushings in the carts suspension simply weren’t up to the extremes of heat and sunlight during the day, blistering cold at night and over-enthusiastic drivers dawn to dusk.
Mis-match a rubber’s ‘personality’ with its purpose and at best you’ll have a failure. At worst a disaster.
Ask us! We can help
Big brands test hundreds of products in extreme locations, but it’s likely that this will be beyond your means. However, you can defend against disaster simply by asking our advice before choosing your rubber product.
To show the kind of unique breaks, scrapes and mistakes that can happen in rubber selection, we made a video. We put different types of ‘seemingly’ similar rubber through a series of extreme tests with surprising results… Check it out when it comes out on our social media channels.
Above: AVMR stretching rubber samples to destruction to guage impact of applied environmental conditions.
Let us get your product right first time. If you’re in need of an extreme solution – no matter how hot, cold, rough, tough or slippery – do give us a call.
If you need advice, please drop us a line at sales@antivibrationmethods.co.uk or Tel: +44(0) 1985 219 032. We’re happy to help.
Related Posts
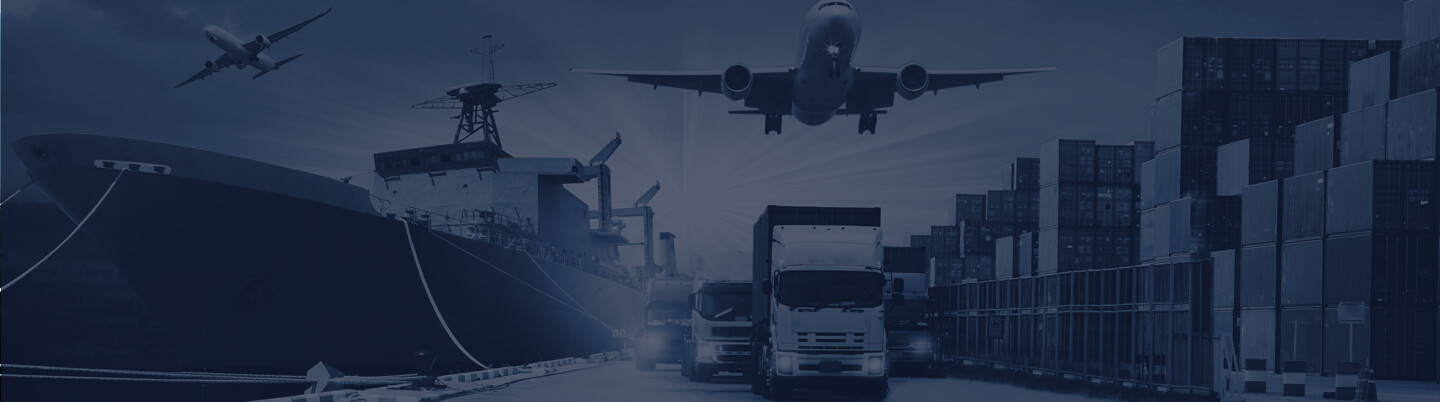
07/03/2023
Challenges in specifying Rubber and Elastomeric Materials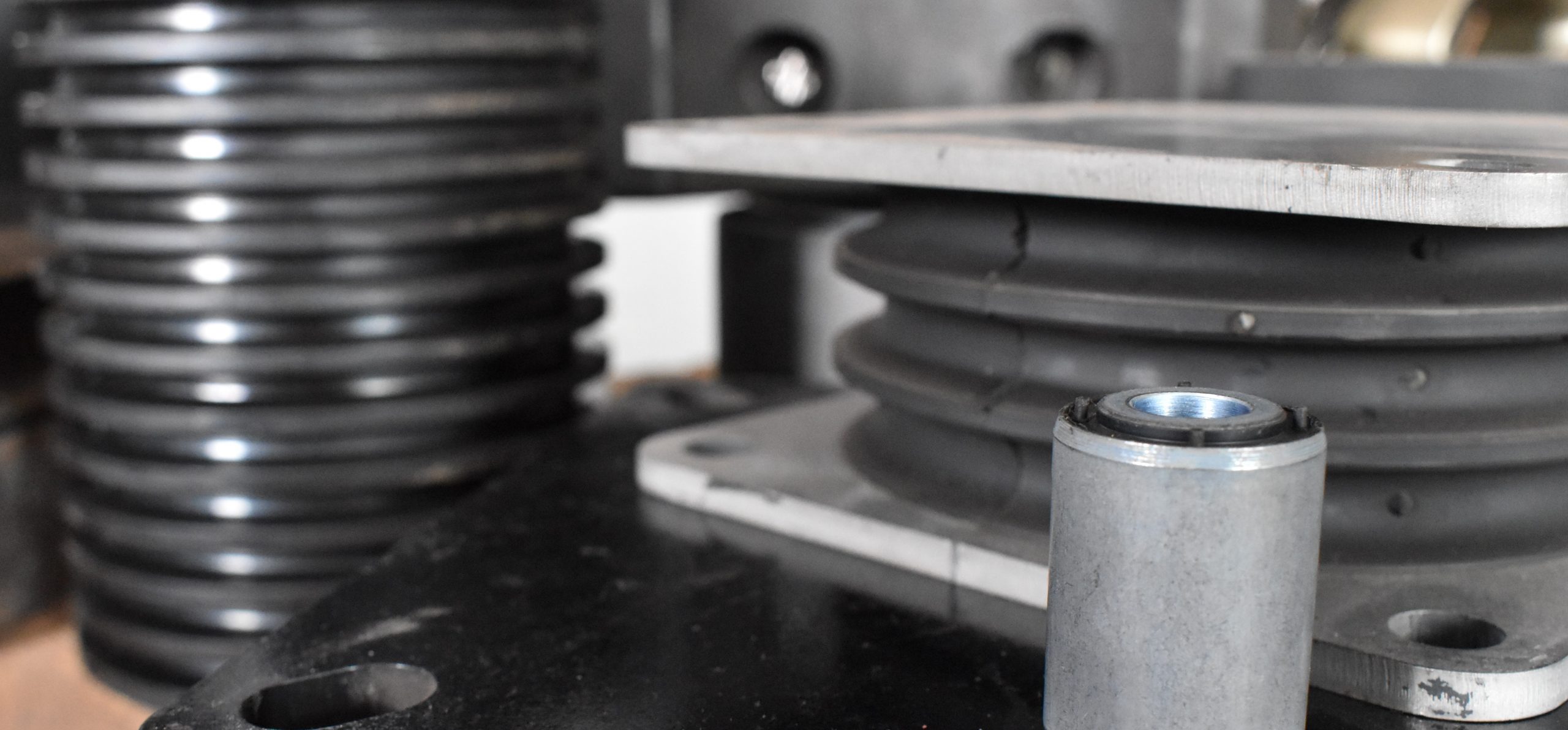
07/03/2023
Natural Rubber Engineering Compounds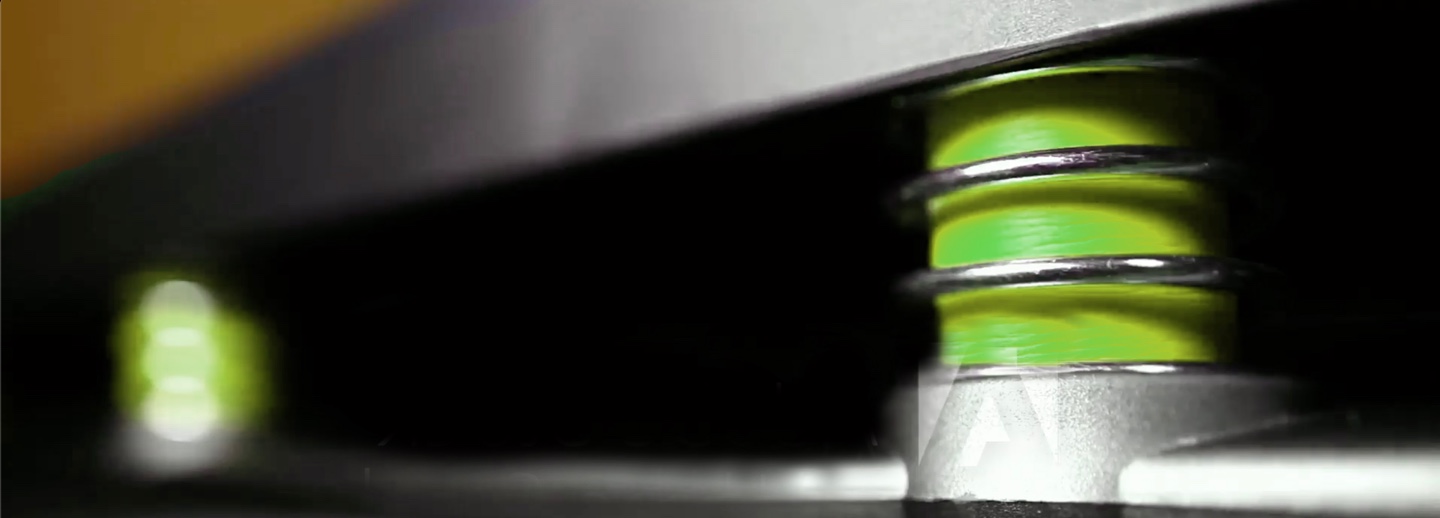
06/26/2023
Heat Generation in Rubber and Elastomers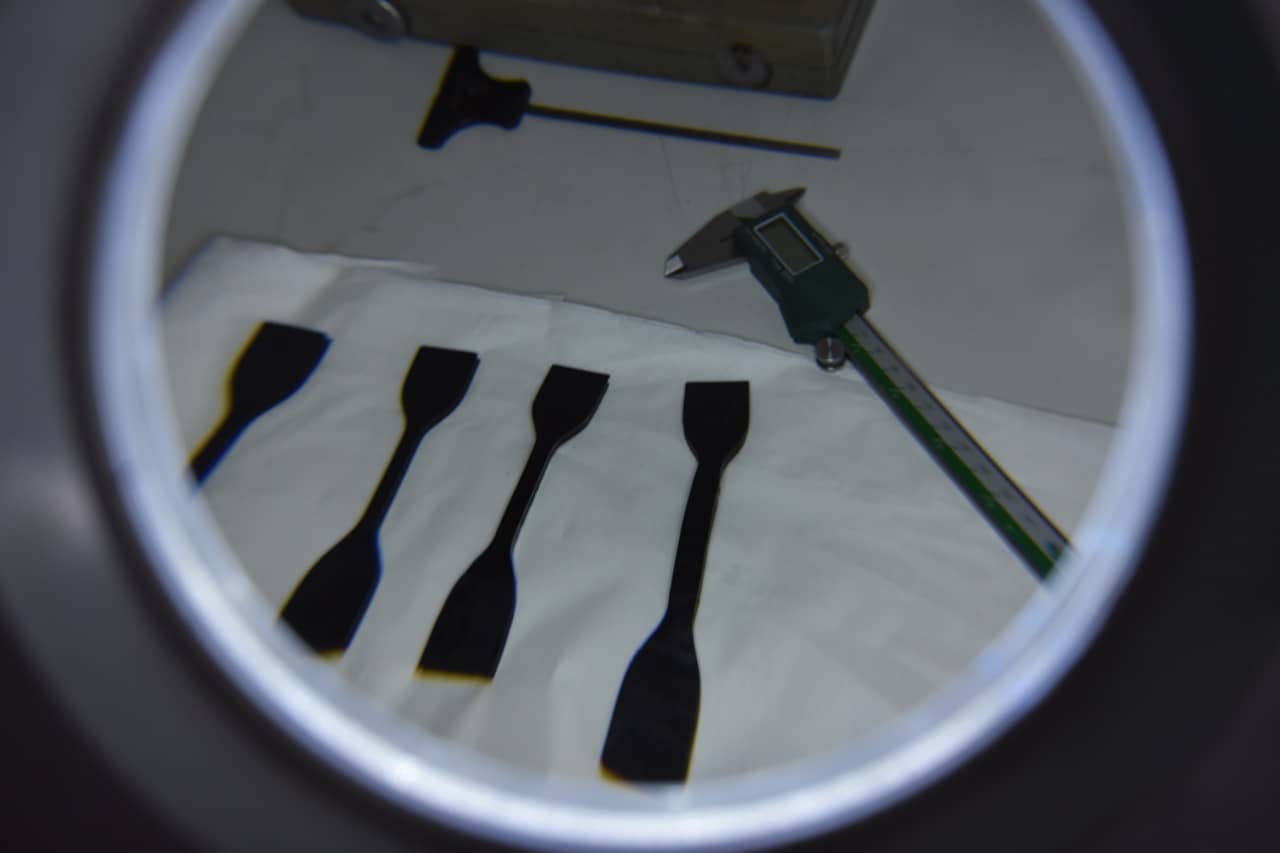
06/12/2023
Stress-Strain Characteristics of Rubber & Elastomers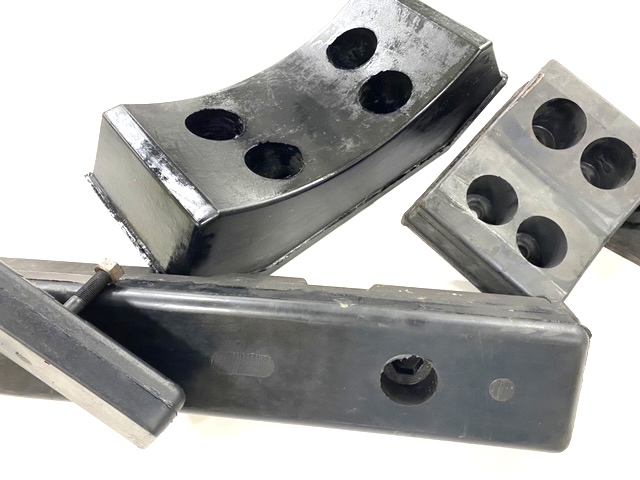
05/22/2023
How to create a strong rubber bond in my product?