10/21/2022
How much do Rubber Moulded products cost?
This is probably one of the most common questions we get asked, I wish there was a simple answer. In lieu of a simple answer, I have broken down of the variables and considerations to help give you an idea. I hope this is interesting and helpful.
I should also add that I can only speak to what AVMR does. We are typically told that our pricing is 10 – 30% lower cost that UK competitors in our industry; we have lost jobs to lower cost suppliers, just not very often. Feel free to give us a nudge if we are not.
We intend to write separate posts giving more detail on the below but if you have specific questions, let us know.
I have ignored product design input and assumed that we have been given product specifications and drawings or models. Key factors impacting price are:
- Mould tool required
- Volume of product required
- Materials used
- Time taken to manufacture
- Quality management relating to the product.
Mould Tooling
To get going we will need a mould tool. In short, these can be £750 or £50,000 for typical items that we manufacture. Based on experience, I can well imagine £500k is possible for a large and complex mould tool.
It is worth bearing in mind that this tool might produce a batch of 200 units in one go (200 cavities), or it might only produce one. Establishing the optimum number of cavities in a tool is a relatively simple calculation, which we will do a separate post on.
There is also time required to commission the tool, which might result in small changes required to the tool if, for example, if the product is particularly precise, we might have to use ‘dead reckoning’ to close in on the tolerances, meaning that the tool will probably have to go through a number of machining operations to get the right final dimensions. The costs associated with this process will normally have been built-in to the tooling price.
Volume of product required
The volume of product affects the price in a few ways:
- Higher volume justifies higher batch sizes in the tool, which makes the tool more expensive, but reduces the production costs.
- Higher volumes reduce material purchase prices, to a point. This applies for any substrates (e.g. steel plates, tubes) and compound (e.g. rubber).
- Any production run requires setting up, which takes time. If we can do longer runs of a product, then the setup time is amortised across a larger volume.
- Certain raw materials that we use can only be produced in certain batch sizes. Hopefully we can use a material or compound which is a stock item so that the MOQs (minimum order quantities) do not impact the price, but we have had projects where the material MOQ was a major cost driver.
- The overhead required to get a project going might be significant in comparison to that required for repeat orders. Therefore, tricky, small and one-off orders will attract a higher level of overhead when compared to long term repeat orders
Materials Used
The easy part of this to discuss is Rubber. For low volumes of relatively normal rubber we are looking at £40/kg to £100/kg for higher volumes (over 60kg) this can quickly drop to £4/kg – £60/kg. Prices will further reduce if we can order in either multiple batches or larger batches, but the improvements from a 60kg batch diminish quickly.
Metal or plastic substrates are another matter; their price spectrum is broad. Factors impacting these prices include:
- If mould or cast tooling is required
- Most of the information in the ‘mould tooling’ section applies here too, although costs for casting are considerably lower, but for plastics are typically higher.
- Material to be made from
- Material prices naturally vary. In addition, they currently volatile too due to energy costs and material availability. Basic steel plates which cost £1.00 five years ago, are now circa £2.50.
- Quantity to be made
- See volume section, which covers the same points.
- Machining required
- This really depends on the complexity and the volume required.
- Plating required
- Pricing here remains fairly predictable depending on the plating used, and the volume as shipping has to be covered.
Time taken to manufacture
We on average, we charge £60/hour (production charge incl. overhead), but the overhead is lower for higher volumes and higher for low volumes. Elements of production which have time allocated to them are:
- Rubber and substrate preparation, if required.
- Moulding
- Trimming
- Post processing e.g. stamping, swaging, sizing, cropping
All other processes are considered as an overhead.
Quality management relating to the product
Whilst there are standard quality checks which accompany each process step, some products require additional checks. If these are related to a quality issue we might have with a supplier, then that is unlikely to impact the customer price, but if the product requires additional tests or paperwork then these will be chargeable.
Related Posts
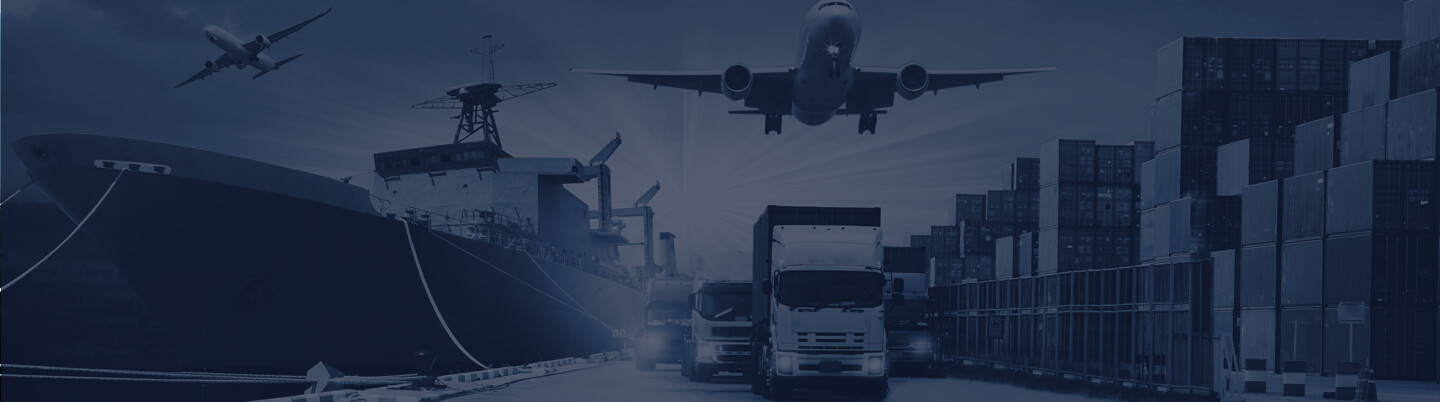
07/03/2023
Challenges in specifying Rubber and Elastomeric Materials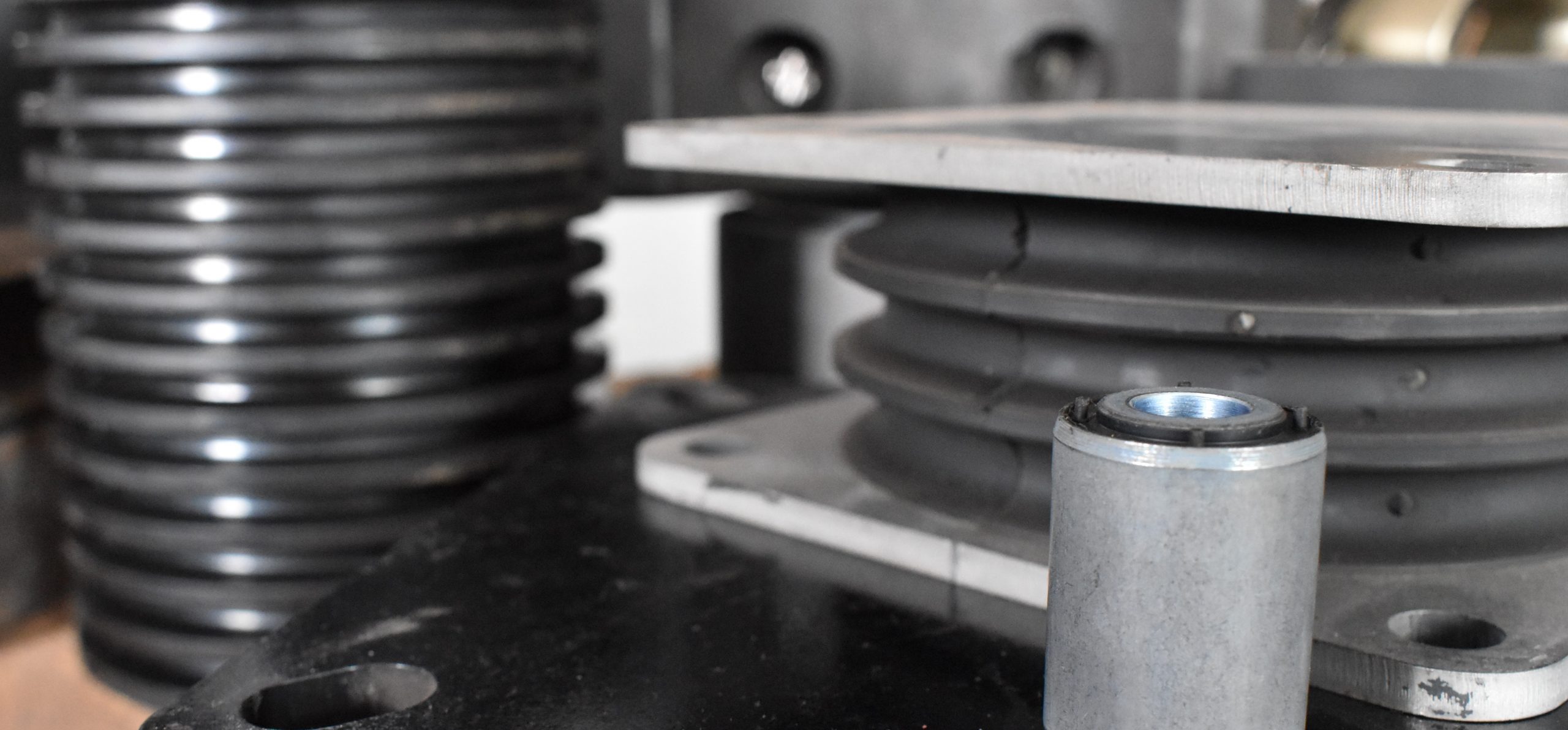
07/03/2023
Natural Rubber Engineering Compounds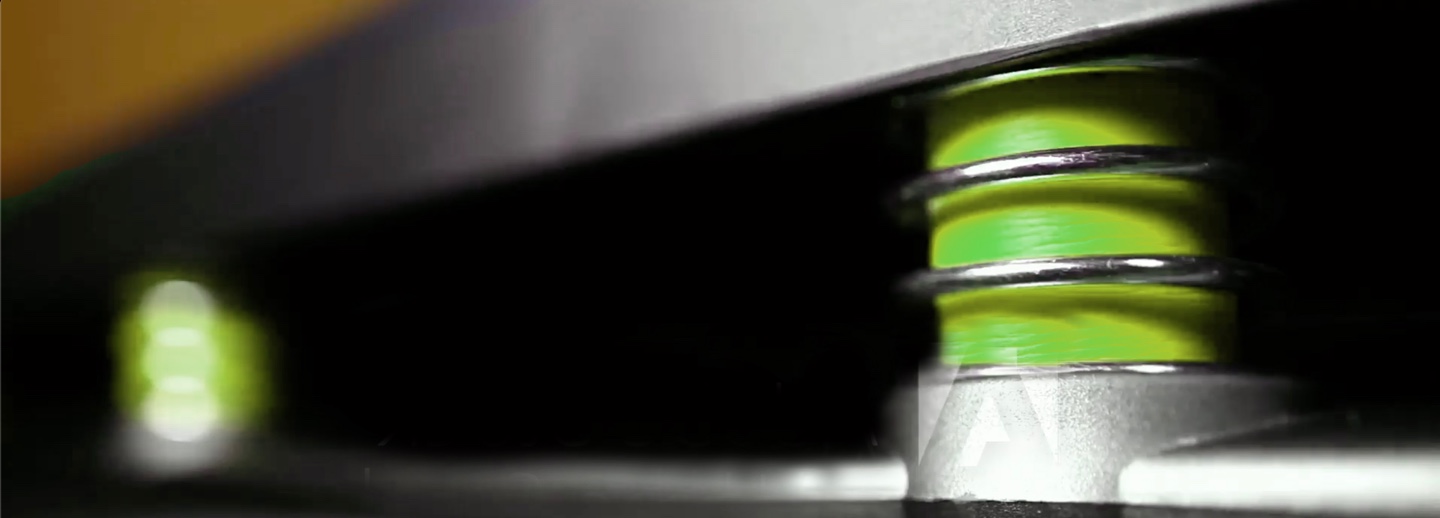
06/26/2023
Heat Generation in Rubber and Elastomers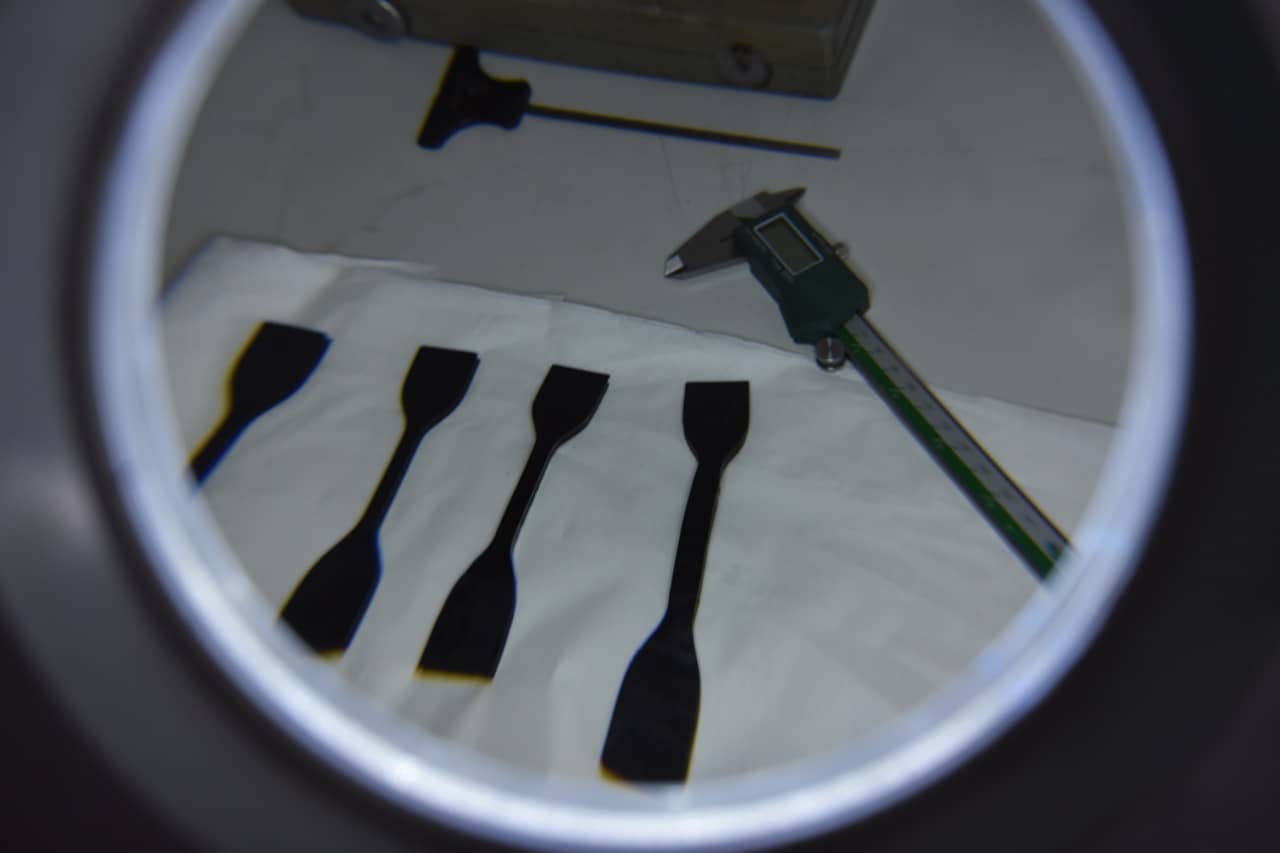
06/12/2023
Stress-Strain Characteristics of Rubber & Elastomers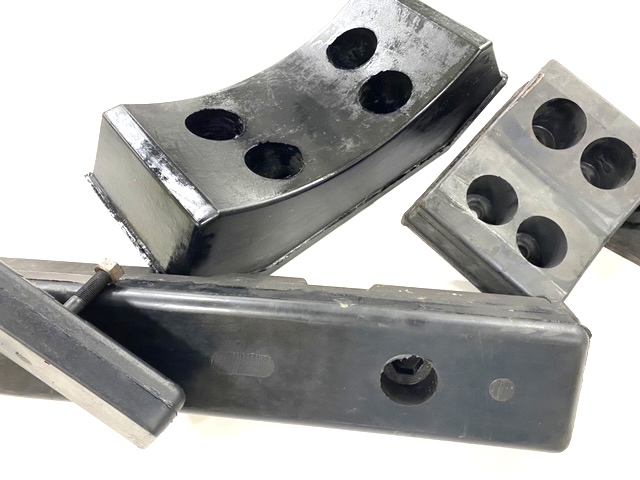
05/22/2023
How to create a strong rubber bond in my product?